Understand the versatility of plastic extrusion in design
Understand the versatility of plastic extrusion in design
Blog Article
Recognizing the Basics and Applications of Plastic Extrusion in Modern Production
In the realm of modern manufacturing, the method of plastic extrusion plays a crucial role. Deciphering the basics of this process exposes the real convenience and possibility of plastic extrusion.
The Principles of Plastic Extrusion Refine
While it might show up facility, the principles of the plastic extrusion procedure are based upon reasonably straightforward principles. It is a manufacturing process wherein plastic is thawed and after that shaped into a continuous account through a die. The raw plastic material, frequently in the type of pellets, is fed into an extruder. Inside the extruder, the plastic goes through heat and pressure, causing it to melt. The liquified plastic is after that compelled via a designed opening, called a die, to develop a long, constant product. The extruded product is cooled and after that reduced to the wanted size. The plastic extrusion process is extensively used in numerous sectors because of its convenience, effectiveness, and cost-effectiveness.
Various Kinds of Plastic Extrusion Methods
Structure upon the basic understanding of the plastic extrusion process, it is essential to explore the different strategies associated with this manufacturing technique. Both primary techniques are profile extrusion and sheet extrusion. In account extrusion, plastic is thawed and created into a constant account, typically made use of to create pipes, poles, rails, and home window structures. On the other hand, sheet extrusion creates huge, flat sheets of plastic, which are commonly further processed into products such as food packaging, shower curtains, and cars and truck components. Each strategy calls for specialized equipment and precise control over temperature and pressure to guarantee the plastic preserves its shape during cooling. Understanding these techniques my review here is essential to using plastic extrusion successfully in modern-day production.
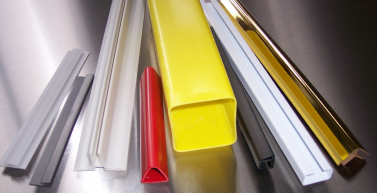
The Role of Plastic Extrusion in the Automotive Sector
A frustrating majority of components in contemporary automobiles are items of the plastic extrusion procedure. Plastic extrusion is primarily used in the production of different auto components such as bumpers, grills, door panels, and dashboard trim. Thus, plastic extrusion plays an essential duty in auto manufacturing.
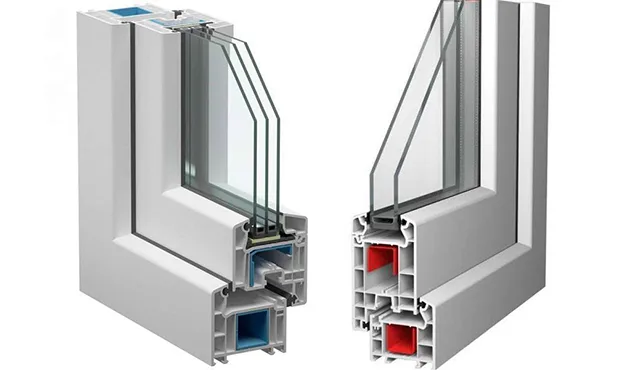
Applications of Plastic Extrusion in Durable Goods Production
Past its significant effect on the auto market, plastic extrusion verifies equally efficient in the realm of customer goods making. The flexibility of plastic extrusion allows producers to design and generate complicated shapes and sizes with high accuracy go to the website and performance. The flexibility, versatility, and cost-effectiveness of plastic extrusion make it a recommended selection for many consumer products suppliers, contributing considerably to the market's development and innovation.
Ecological Influence and Sustainability in Plastic Extrusion
The prevalent usage of plastic extrusion in manufacturing welcomes examination of its ecological effects. Effective equipment minimizes energy usage, while waste administration systems reuse scrap plastic, reducing raw product needs. Despite these enhancements, even more technology is needed to mitigate the ecological footprint of plastic extrusion.
Final thought
In conclusion, plastic extrusion plays a crucial duty in contemporary manufacturing, specifically in the automobile and consumer products fields. Recognizing the essentials of this process is essential to enhancing its benefits and applications.
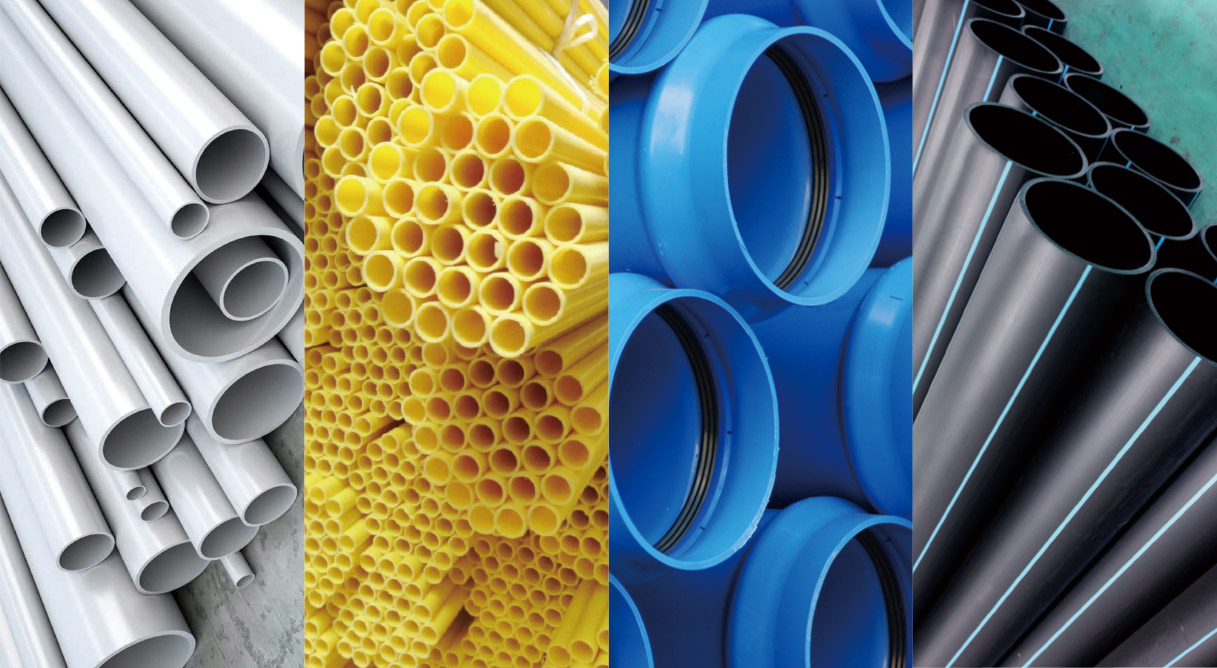
The plastic extrusion process is thoroughly utilized in various markets due to its performance, adaptability, and cost-effectiveness.
Structure upon the basic understanding of the plastic extrusion procedure, it is required to explore the numerous techniques involved in this manufacturing approach. plastic extrusion. In comparison, sheet extrusion develops huge, level sheets of plastic, which are usually more refined into products such web link as food packaging, shower curtains, and cars and truck parts.A frustrating bulk of components in modern-day lorries are items of the plastic extrusion process
Report this page